CEMENT TERRAZZO BLOCK PRODUCTION STAGES
For specific technical enquiries, please contact the In Opera Technical team.
What is terrazzo?
Terrazzo is made by mixing stone, marble and granite together with a binding agent. Its traditional ingredients are cement mixed with marble powder and an aggregate material.
In everyday language, the term ‘terrazzo’ is used to define various marble and stone agglomerated materials, including the ones with cement, resin, or epoxy binders. However, cement is the traditional binding agent used for terrazzo blocks. And in the EU, the technical standards of the material and their legal implications are determined around this type of terrazzo only.
Terrazzo is commonly used for indoor flooring, but the possibilities are much broader, it can be used for interior or exterior wall cladding, furniture surfaces and a wide range of landscaping applications for commercial or domestic projects.
When it comes to choosing terrazzo, it is essential to understand the methods and process of producing terrazzo to get the most out of the material’s possibilities, both technically and aesthetically.
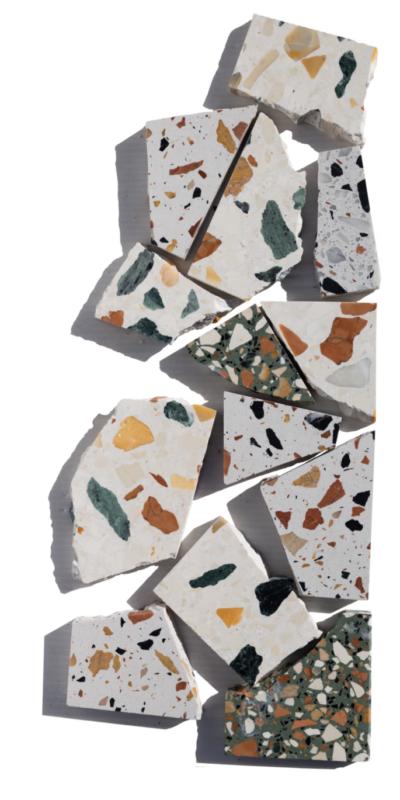
PREPARING TERRAZZO AGGREGATE & BASE
A. Mining marble and stone chips
Marble and other quarry waste material are extracted and taken to aggregate processing plants.
B. Stones are processed by colour
Boulders and stones of different types and colours are processed separately, thus preserving the original colour of the natural material.
C. Sorting by size
Boulders are crushed into ‘stone chips’, aka aggregates of various sizes.
D. Granulating
The crushed aggregates are passed through sieves of various grades that categorises them into standardised sizes. Larger aggregates are used as terrazzo stone inserts, whereas the finest sand and dust granules make up the main component of the terrazzo base.
E. Cleaning
Chips are washed thoroughly to get rid of dust and other unwanted particles. This prevents dust contamination between different coloured stones.
PRODUCING TERRAZZO BLOCKS (in a vacuum)
Any terrazzo design follows a strict recipe with a precise ratio between stone granules, chips, binders and other ingredients.
A. Mixing & Moulding
Terrazzo components, which are stored separately in hoppers, are loaded into large containers. They are taken into a vacuum environment, where the ingredients are mixed, poured into metal moulds for terrazzo blocks. This prevents any air bubbles contaminating the final terrazzo material.
Finally, the terrazzo mixture is vibrated and left to settle in a vacuum in order to remove the remaining unwanted air bubbles. The process is fully automated and precisely navigated from the control room.
B. Settling and Curing
The block is cured for 28 days for the material to fully solidify. After which, it can be cut into slabs or many other solid custom shapes.
Technical information
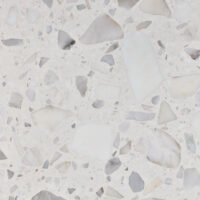
CEMENT AGGLOMERATE
Standard terrazzo ingredients:
- approx.10-15% white cement, used as a binder;
- mixed with white Carrara powder, aka Calcium Carbonate.
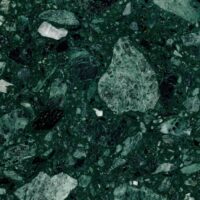
RESIN AGGLOMERATE
It consists of 93% marble chipping and just 5-7% of the resin binder.
The tiles are thinner, thus, lighter in weight than terrazzo cement.
CUTTING BLOCKS INTO SLABS
Blocks can be cut into slabs, as well as carved into custom shapes, making terrazzo blocks suitable for creating custom landscaping features or large decorative objects, such as furniture or sculpture.
A. Cutting blocks into slabs
The cured block is cut into slabs using a gang saw. The saw has a large number of parallel blades, cutting at the same time. To cut a single block into slabs, it takes around 4 hours.Â
Water is used to keep the blades cool and dust-free. Terrazzo factories mainly use rainwater for the cutting process, after which the water gets filtered and recycled throughout the rest of the slab preparation process.
B. Polishing
The slabs are put through a polishing machine which can be adjusted to achieve various finishes to meet specific project requirements.
C. Treatment
The slab is treated with an impregnating sealer that helps to protects the terrazzo from staining.
EXCHANGE SQUARE
SEMAPHORE
CUTTING SLABS INTO TILES
A. Cutting & Shaping
Ready slabs are cut into smaller-sized tiles. Slabs can also be cut in any other geometric shape to create intricate design features.
B. Rectification & Polishing
The edges of the tiles are rectified through a honing process to ensure the accuracy of the final material size and dimensions.
Individual tile pieces are calibrated to achieve an accurate thickness and surface texture.
C. Quality control & Packaging
Each tile goes through manual quality checks. After which, the tiles are packaged and made ready to be shipped to clients.
Standard size guideline
*Each block and slab vary in size depending on the type of material. Please consult our technical team for further info.
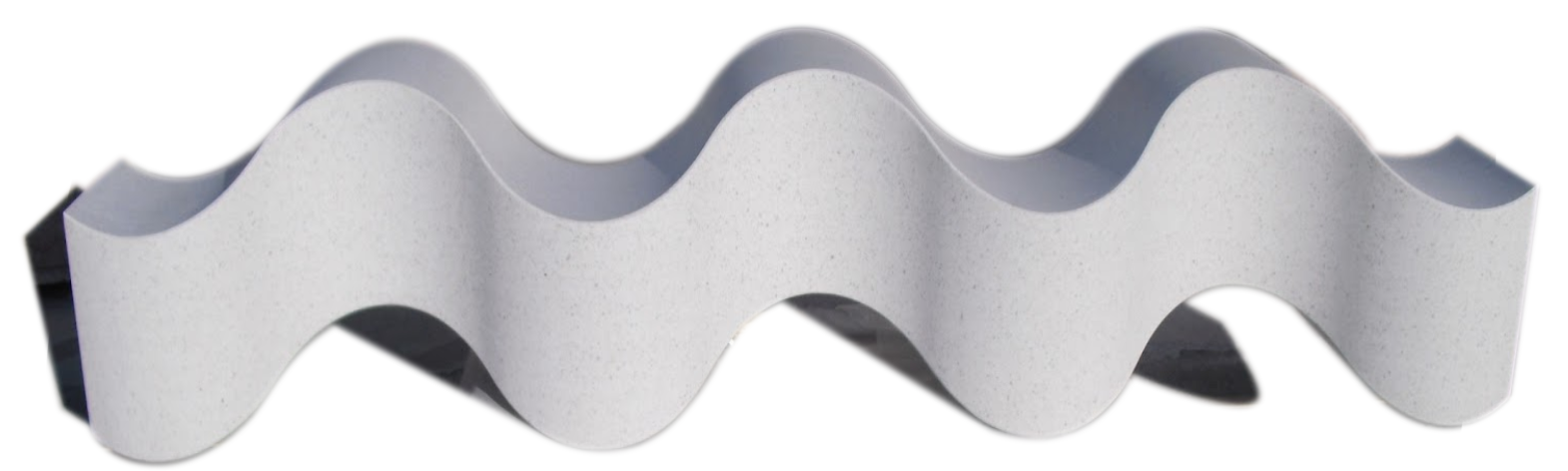