TERRAZZO SPECIFICATIONS & DESIGN
For specific technical enquiries, please contact the In Opera Technical team.
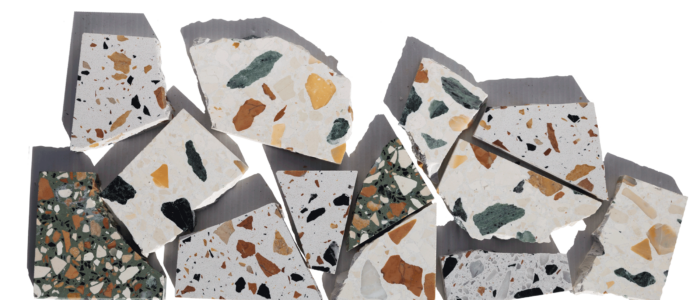
Why choose terrazzo?
Terrazzo is a material which offers endless design possibilities whilst retaining its original quality for many years. It is suitable for a broad range of interior and exterior applications including flooring, interior and exterior wall cladding, furniture surfaces and a wide range of landscaping applications for commercial or domestic projects.
When choosing terrazzo, it is important to understand the production and design process to get the most out of the material’s possibilities. Below we cover the essential points in terrazzo specifications and design, specific to the EU standards of production and application.
TERRAZZO PRODUCTION
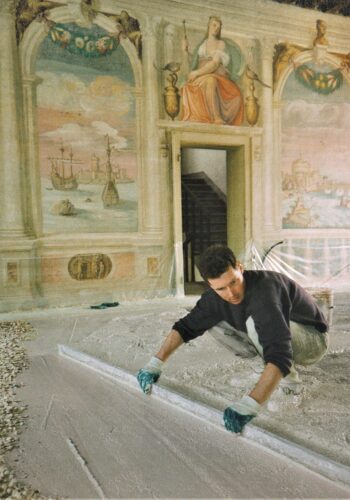
Terrazzo, dates back to very ancient times. Historically, some say marble quarry workers created terrazzo – by taking the ”crumbs“ of their work home, mixed them with a mortar, and paved their terraces in situ.
Regardless, Venetian terrazzo became prominent from the 1400’s onwards, culminating with the production of pressed terrazzo tiles around the 16th century in Northern Italy, which has some of the biggest marble quarries in Europe. During the industrial boom in the 60s, the tiles were either mechanically pressed or cast by hand.
Shortly after the method has evolved into casting large-sized terrazzo blocks and slabs; the materials undergo rigorous quality control checks to meet the demands of the current industrial scale.
The difference between the block-cast and mechanically pressed terrazzo is that the former is superior to the latter in terms of its technical performance.
In addition, due to our patented manufacturing process in a vacuum, the terrazzo produced in a block is denser, thus more durable and consistent in colour and appearance, which makes it suitable for large-scale architectural projects.
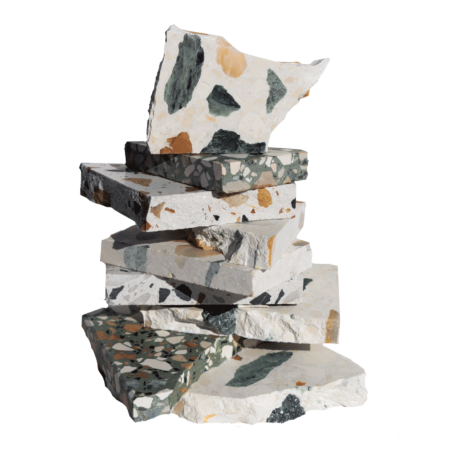
What does terrazzo consist of?
Terrazzo hasn’t changed much, in terms of it’s consistency, since it’s origin. The standard ingredients are: a mixture of stone aggregates, mostly marble ( or it can also be granite, quartz, or glass chips), marble powder, and a binding agent.
Cement is the traditional binding agent used for terrazzo. It can also be made using alternative binding agents, such as resin or epoxy. However, this type of agglomerate material isn’t considered an authentic terrazzo. However, it can be a good solution for clients seeking specific technical performance values that traditional cement agglomerate terrazzo lacks.
BINDING AGENTS
When choosing terrazzo, apart from focusing on the obvious design components, such as the colour and the stone aggregates, we suggest considering the difference between the two binding agents used for terrazzo – Cement and Resin.
The binding agent determines many physical properties of the final terrazzo, such as the thickness and weight of the tiles and slabs and even the size of the stone chips it can hold.
In everyday language, the term ‘terrazzo’ is used to define various marble and stone agglomerated materials, including the ones with cement, resin, or epoxy binders. However, cement is the traditional binding agent used for terrazzo. And in the EU, the technical standards of the material and their legal implications are determined around this type of terrazzo only.
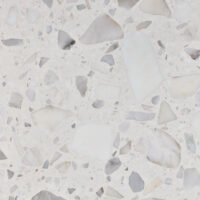
CEMENT AGGLOMERATE
Cement is the traditional binding agent used for terrazzo.
Cement agglomerate terrazzo is highly durable, can withstand any weather conditions, and can be manufactured to limit colour fading.
Terrazzo with a cement binder can hold stone chips up to 40 mm.
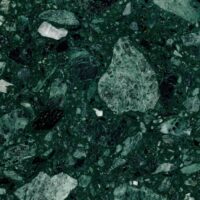
RESIN AGGLOMERATE
Resin agglomerate ‘terrazzo’ consists of 93% marble chipping and 5-7% resin.
The tiles can be thinner, thus, lighter in weight than the terrazzo-cement.
It can hold stone chips of up to 80 mm in diameter.
BASE COLOUR
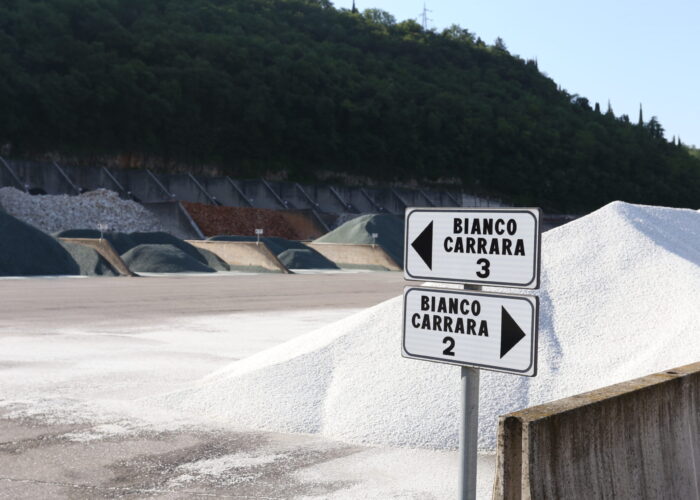
Terrazzo combines the organic texture of natural stone and the plain colour background of the base. The base consists of marble dust and other pigments.
Bianco Carrara marble with pure and cool shade serves best as the base material. The whitest particles of the Carrara marble are ground into a fine powder, also known as Calcium Carbonate.
Most of our standard tile ranges consist of terrazzo with a natural marble base; for example, we use the powders of Rosa Corallo marble for a terrazzo with a pink-coloured base.
The base can be closely matched to many colours in the RAL chart.
AGGREGATES
The other main component of terrazzo is the stone chips or aggregates. Marble is the most popular choice of all other materials, but you can get creative here and mix glass, shells, recycled porcelain, and even recycled terrazzo.
The aggregates can be as small as MK000 (smaller than 0.7 mm) to 40 mm in diameter for cement and up to 80 mm for resin terrazzo.
Generally, the standard chip sizes are categorised from MK000 to N8 (40 – 50 mm); see below:
BESPOKE
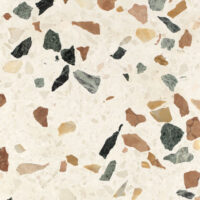
VENETIAN TERRAZZO
Terrazzo that contains stones bigger than the standard aggregate size is called Venetian terrazzo. It’s one of the oldest versions of terrazzo made by a method of seminato, a term that derived from an Italian word for ‘seeding’.
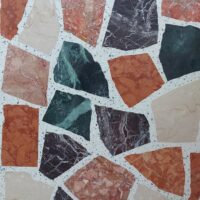
PALLADIANA TERRAZZO
Palladiana terrazzo, on the other hand, is suitable for achieving a more paver-like effect with a polished finish, where flat pieces of marble slabs are used instead of stones.
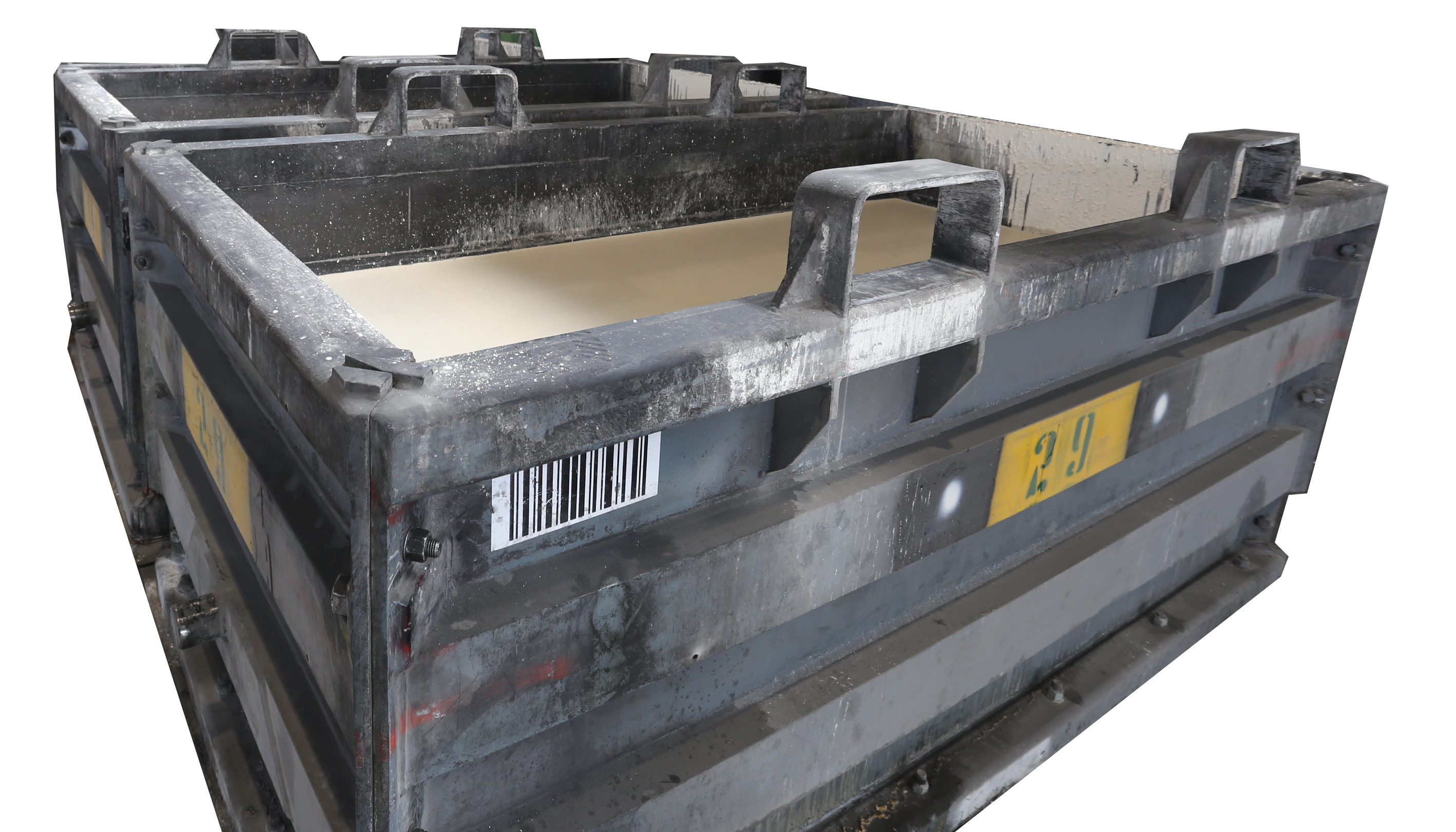
How is terrazzo produced?
Terrazzo is produced in blocks and slabs, cast in large-sized moulds; the materials undergo rigorous quality control checks to meet the demands of the current industrial scale.
Due to our patented manufacturing process in a vacuum, the terrazzo produced in a block is denser, thus more durable and consistent in colour and appearance, which makes it suitable for large-scale architectural projects.
BLOCK PRODUCTION
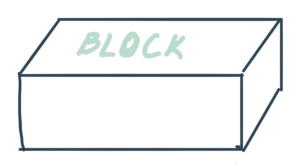
Most of the terrazzo supplied in the industry is now produced in blocks. Ingredients for specific terrazzo are taken into a vacuum chamber, mixed, poured into a block mould, after which the mixture is vibrated to eliminate air bubbles. Once the block is removed form the vacuum chamber, it is left to cure until the concrete is fully strengthened. For cement agglomerate terrazzo, this process takes about a month and up to two weeks for resin. The method achieves a homogeneous surface colour and consistent texture throughout the block, making it the perfect process for large-scale projects.
Once ready, the block is cut into slabs, standard-sized tiles, or other geometric shapes. It can also be carved into any other 3d form.
HAND CAST TERRAZZO SLABS & TILES
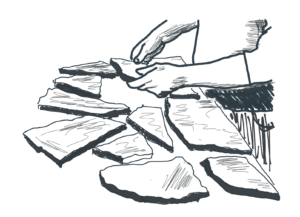
More intricate terrazzo design will require a traditional hand cast method, pouring the mixture into bespoke moulds and cured before being rectified to the required size and thickness, ground, and polished. This process requires meticulous attention to consistency and colouration; hence, it takes longer to produce. However, it results in a terrazzo tile that is easy to install and looks like it’s been installed in situ.
Within our group, we only produce high-quality hand-cast terrazzo using a patented vacuum system, which eliminates air bubbles and improves colour consistency.
IN-SITU TERRAZZO
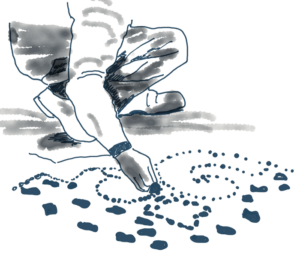
It’s a manual process where the terrazzo mixture is poured on-site, after which it is ground and polished to the required finish. It is a difficult, hence, ‘dying’ trade, which can be executed only by specialist installers.
Therefore, the method might not fit the modern, fast-paced construction process. And careful consideration should be given to the construction program and budget when installing terrazzo in situ.
Nevertheless, the result is beautiful and smooth flooring, which is impressive in terms of design and much easier to maintain than tiled floor joints filled with grout. Hence, demand for the material grows from year to year.
MECHANICALLY PRESSED TERRAZZO
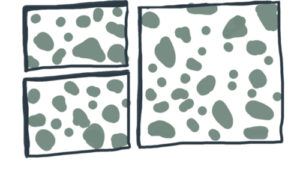
Mechanically pressed terrazzo tile production originated in 16th century Italy and spread wider in the 60s on an industrial scale.
These tiles can be manufactured in a single or double layer, the latter consists of sand and cement. The individual tiles were hydraulic pressed into moulds.
This method can no longer meet modern design and technical specifications due to its limited size and design possibilities and is not commonly used in mainstream industrial construction.
TERRAZZO FINISHES
Once the terrazzo blocks are cut into slabs, the slabs are put through a polishing machine which can be adjusted to achieve various finishes to meet specific project requirements. They are also chemically treated with an impregnating sealer to protect and prevent the terrazzo surface from staining.
There are many ways the finishes can be tweaked and adjusted to meet many slip-resistance requirements. However, the following are the most common types of finishes widely used throughout the industry.
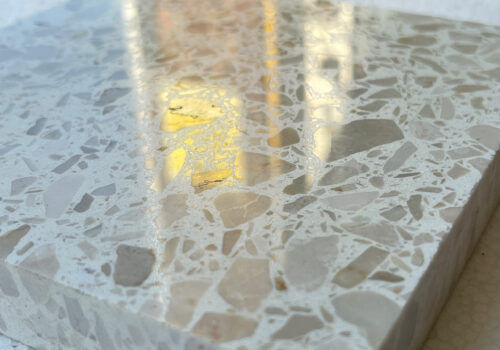
POLISHED
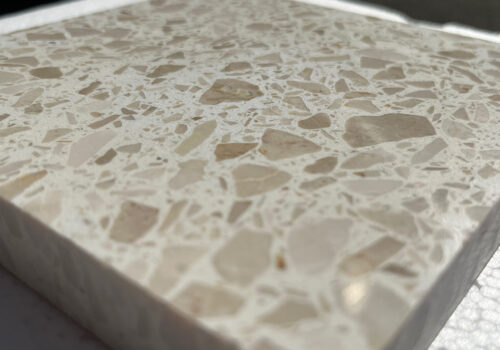
HONED
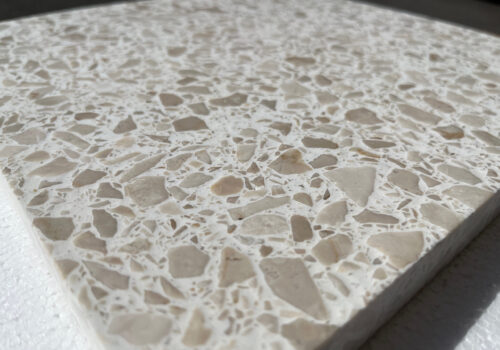
BRUSHED
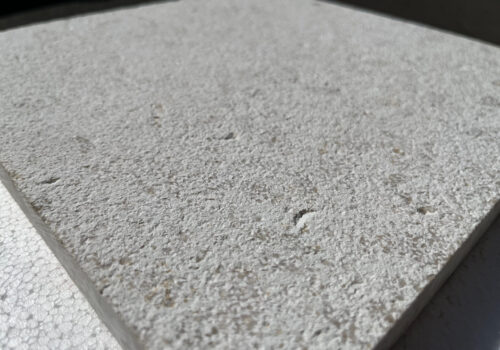
SANDBLASTED
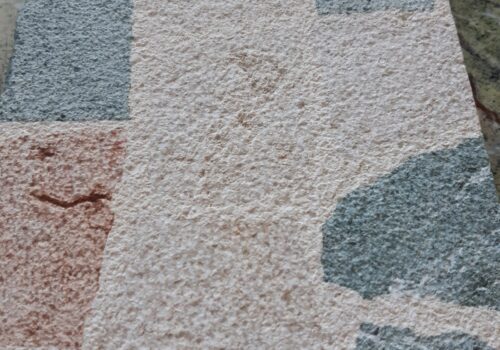
BUSH-HAMMERED
It is highly slip-resistant and is suitable for outdoor and wet areas.
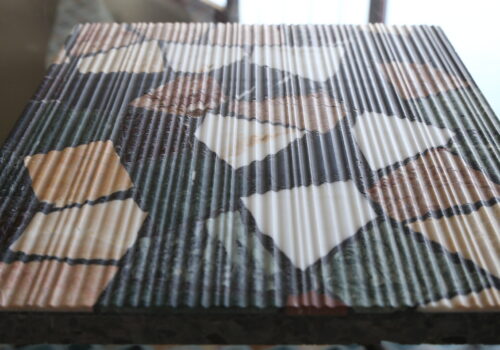
BESPOKE FINISH
TILE GROUT & DIVIDING STRIPS
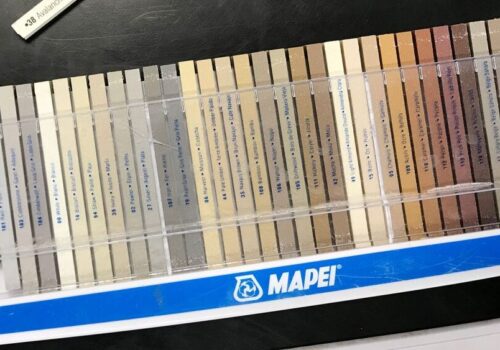
GROUT
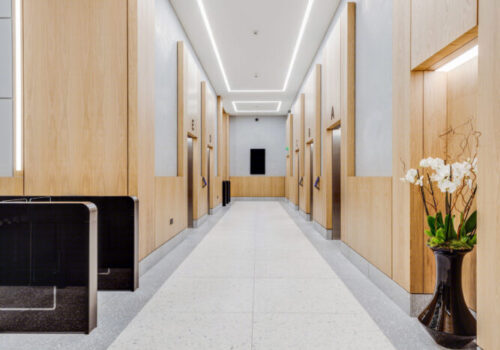
DIVIDING STRIPS
For cement-based terrazzo, dividing strips must be laid in grids.