STAGE 1/4
A.
InsideĀ marble quarry, Verona, Italy, 2022.
Mining marble and stone chips.
Marble and other quarry waste material is extracted and taken to aggregate processing plants.
B. & C.
Sorting stones by colour and size.
Stones of different types (marble, granite, etc.) and colours are processed separately.
Boulders are crushed into stone chips, also known as, aggregates, of various sizes, with the largest range being 40 mm.
D.
Cleaning.
Chips are washed thoroughly to get rid of dust and other unwanted particles. This prevents dust contamination between different coloured stones on the site, ensuring clean and precise colouration in the final terrazzo.
For terrazzo with resin binder (as opposed to cement) the chips must be fully dried after washing.
An opto-electronic system, with high-speed cameras and an air nozzle deflecting barrier, fully removes any impurities from the chip mass and sets aside the whitest particles of the Carrara marble to be ground into the base powder, aka Calcium Carbonate.
E.
Granulating.
Left-over chips are further ground into sand granules of various colours, which make up the main component of the terrazzo base. Carrara Bianco marble with pure and cool shade serves best as the base material.
The granules are passed through a series of sieves and are separated into different size grades, with the smallest range being 00.00 - 0.15 mm and the largest 40 mm.
The granules are passed through a series of sieves and are separated into different size grades, with the smallest range being 00.00 - 0.15 mm and the largest 40 mm.
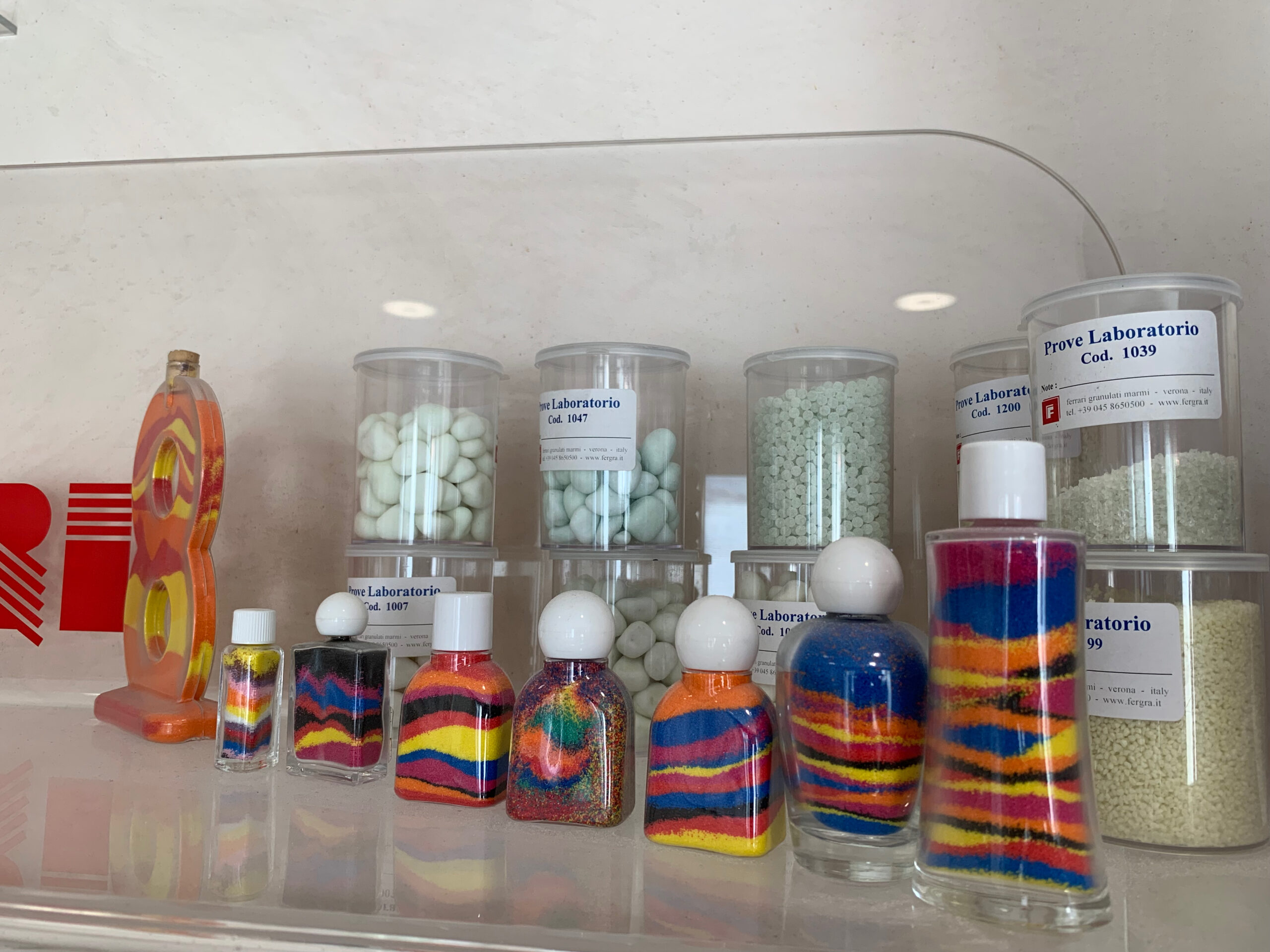
Custom colouring.
Marble granules, used for preparing the base of terrazzo, can be customized to any colour on RAL colour chart.
Dedicated team for Techinical and Design consultation